With a sprawling 100,000-square-foot factory, U.S. Continental stands as a leading private label leather and fabric care company globally. With an unwavering commitment to providing complete care solutions, U.S. Continental has become the trusted partner for leading franchise brands seeking top-tier commercial packaging and private label care product services. The company has enjoyed tremendous growth over the three decades it’s been in business. In that time, the company has become familiar with the hurdles intrinsic to manufacturing: supply chain disruptions, soaring labor costs, and the relentless pursuit of streamlined operations and heightened productivity.
Enter Cyngn's Autonomous DriveMod Stockchaser. After a brief integration period, the DriveMod Stockchaser began transporting pallets around U.S. Continental’s Corona, California facility, doing supply runs between two buildings. Over several months of operation, Cyngn’s self-driving vehicle enhanced operational speed, fostered organizational precision, and delivered substantial labor savings. The vehicle is 4x more efficient than a human driver and even enabled a former forklift driver’s promotion.
According to U.S Continental's VP of Technical Services, Dave Hoover, "U.S. Continental conducts manufacturing operations leveraging two separate, but adjacent facilities. Before deploying the Cyngn autonomous vehicles, we moved pallets of materials one at a time across the parking lot using standard forklift trucks. Now, we move four pallets at a time and do not tie up our staff transporting materials around the oproperty. The production team receives staged materials more efficiently and our warehousing team is free to address more value-add processes, such as cycle counting, order pulling and receiving/put-away. The program has also resulted in the opportunity to promote staff to new and more challenging positions.”
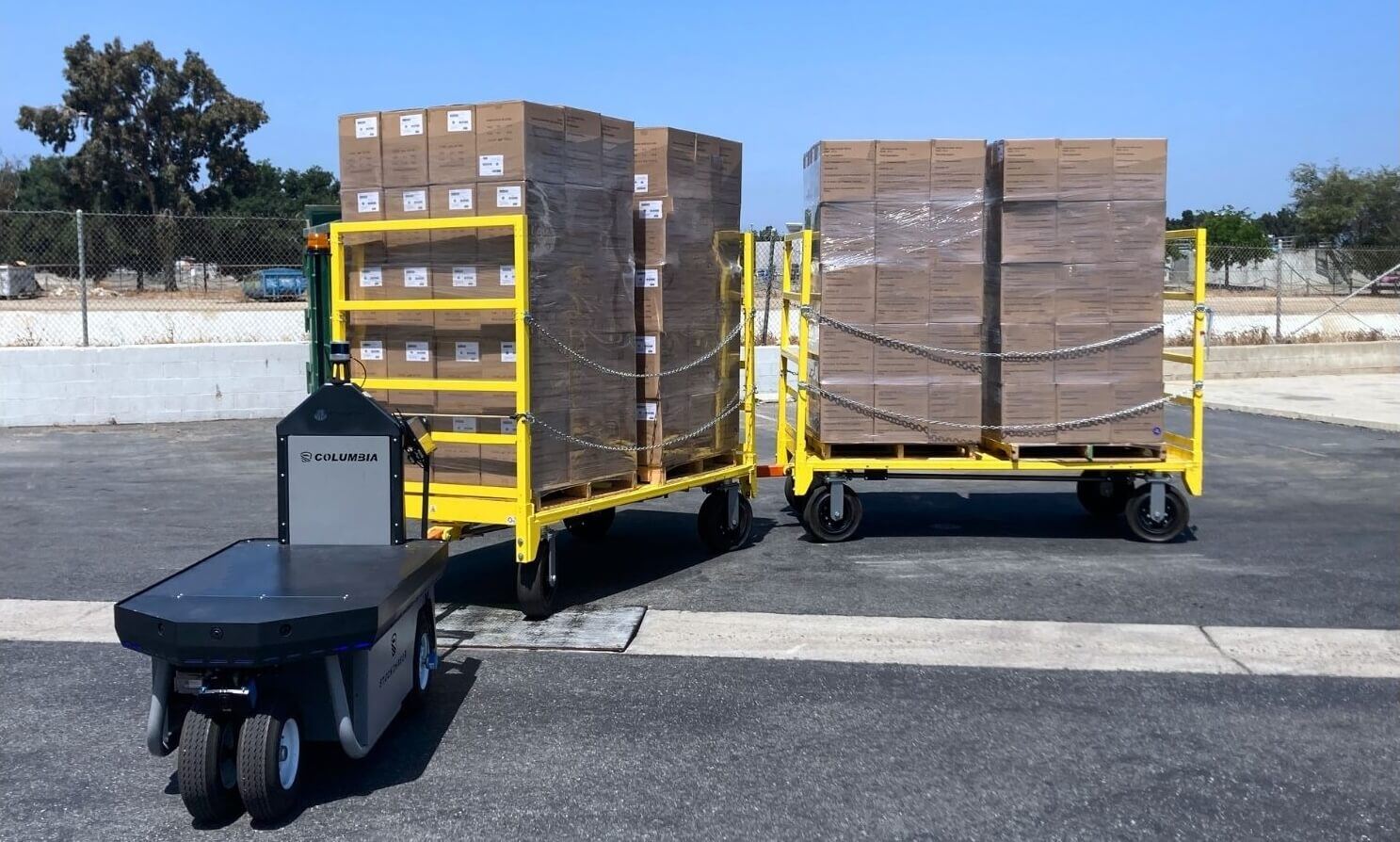
Approach
Deploying Cyngn’s DriveMod Autonomous Vehicle technology at U.S. Continental, involved a simple, yet robust set of steps:
-
Conduct a site assessment. First, Cyngn interviewed U.S. Continental’s operations managers to obtain a thorough understanding of U.S. Continental’s process flows. Then, Cyngn’s field engineers surveyed U.S. Continental’s facility to document the operational design domain (“ODD”) including the lighting, lane widths, and types of obstacles the vehicle could encounter. From this, Cyngn was able to identify transporting pallets from their inventory warehouse to their production facility as the optimal use case for the deployment.
-
Map the facility. In order for an AV to operate, it must know where it is within its environment. First, Cyngn scanned the entirety of U.S. Continental’s facility to create a detailed digital representation of the physical world. The Autonomous DriveMod Stockchaser uses this map to localize and safely operate within the environment.
-
Bring up the vehicle. Once the map was created, Cyngn worked with management to define the vehicle’s operating rules, which included the routes the vehicle would take, the stops where pallets would be loaded and unloaded onto the vehicle, and permissible driving zones.
-
Train key personnel. Finally, before the vehicle was brought into full autonomous operation, Cyngn trained U.S. Continental employees on safe use of the vehicle. Then, the vehicle was seamlessly integrated into their daily workflow.
Throughout the deployment period, the vehicle continuously collected data on vehicle usage and labor productivity in real-time. This data was used both to effectively monitor the vehicle’s performance as well as to eventually calculate cost savings.
Curious to see our bring-up process in action? Watch it here.
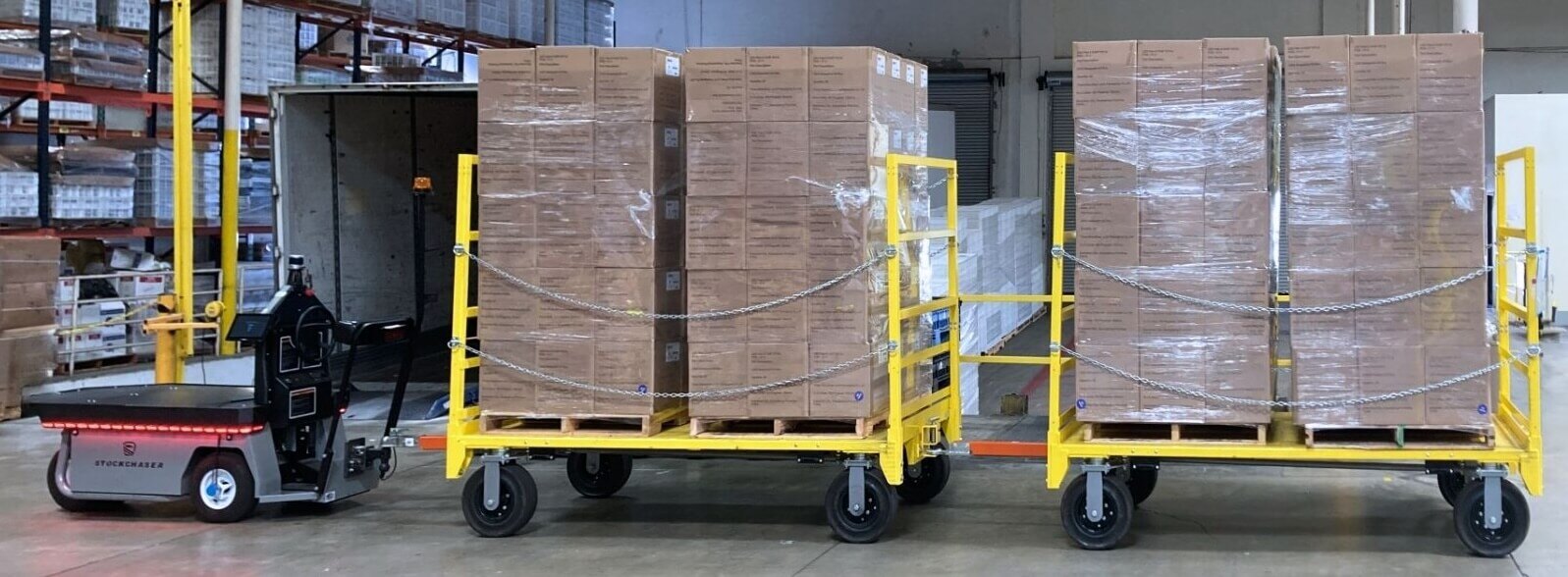
Results
Since kicking off its deployment in March of 2023, the Autonomous DriveMod Autonomous Stockchaser produced:
-
4x Gains in Efficiency. Previously, a substantial human effort of 200 trips per week was required to fulfill pallet delivery between the two buildings at U.S. Continental. However, after the introduction of our autonomous vehicle, this workload has been seamlessly absorbed. Our vehicles surpass traditional manual labor, as they can transport four pallets in a single trip, as opposed to one pallet at a time that can be accomplished with a forklift. This not only multiplies efficiency, but also allows for labor to be reallocated to other more valuable tasks, such as order picking and pulling.
"The additional capacity to move materials from location to location has reduced maintenance costs on our lifts," said U.S Continental's VP of Operations, Lockland Corley. "Every trip the autonomous vehicles make eliminates three additional trips for our forklifts. Our facility transfers raw materials from one warehouse to a second production warehouse, approximately 75 yards one way. Not having to run our forklifts outdoors across the bumpy parking lot has reduced routine wear and tear of our forklifts.”
-
Reallocation of Labor. Beyond operational enhancements, the integration of our autonomous vehicles has sparked positive developments in their workforce. Opportunities for employee growth within the company have emerged, leading to promotions and role reallocations. Employees are now empowered to take on different responsibilities, contributing to a more versatile and skilled workforce. Importantly, this evolution in job roles has translated into increased pay for individuals, highlighting that autonomy is more about task reallocation and the creation of new opportunities than job displacement.
-
Increased Organizational Precision. Teams working directly with the autonomous robot revised their workflows to better align with the vehicle’s predictable schedule. This simple change made a big difference - reducing variability, boosting overall efficiency, and making it easier to train new employees.