In the ever-changing industrial landscape, Automated Guided Vehicles (AGVs) are revolutionizing the way that work gets done, becoming increasingly popular in modern-day logistics, manufacturing, and warehousing. From assembling products to efficiently transporting pallets around a facility, AGVs are tailored to each organization's needs.
In recent years, automated guided vehicles have become smarter and as a result, have emerged as an invaluable tool in complex industrial environments by autonomously moving materials with minimal human intervention. As a result, AGVs have been benefiting organizations across a wide range of industries.
Consequently, the AGV market is projected to grow to $3.3 billion by 2028 — a substantial leap from the 2.4 billion recorded in 2023.
In this article, we'll take a closer look at AGVs, what they do, where they're used, and how they're making a significant impact on numerous industries.
What are Automated Guided Vehicles (AGVs)?
AGVs are self-guided automated vehicles designed to autonomously transport materials in industrial environments, including warehouses, factories, and other facilities. Instead of relying on a human operator, they use a combination of sensors, software, and navigation technology, following predetermined routes such as magnetic tape and painted lines. Therefore, AGVs are similar to how a train follows a fixed track.
AGV vs. AGV System
While an AGV refers to an individual mobile robot, we can also look at automated guided vehicle systems, which encompass the entire infrastructure involved in the deployment, management, and integration of multiple AGVs within a facility. For example, AGV systems are commonly integrated with Warehouse Management Systems (WMS). This integration allows AGVs to receive task assignments and seamlessly communicate with various facets of warehouse operations.
Elements of Automated Guided Vehicle Systems
The elements of AGV systems consist of different self-driving, navigation, and collision warning elements that work together to automate the movement of goods in industrial environments.
Autonomy
The development of self-driving technology marks a significant breakthrough in industrial automation. Thanks to the advancement of technologies like artificial intelligence (AI), machine learning algorithms, and advanced sensors, autonomous vehicles can utilize self-driving functionalities to navigate and operate along fixed paths with little human intervention.
The ability for these autonomous guided vehicles to self-drive doesn’t just make work faster, but it also makes it safer. For instance, an autonomous AGV tugger in a warehouse equipped with self-driving capabilities can intelligently navigate through aisles, avoiding obstacles and optimizing the transportation of goods.
Navigation
Navigation involves the technology and software that enables precise and efficient movement of AGVs. AGV systems typically use a combination of lasers, magnets, and vision technology to guide AGVs along their fixed paths. These methods, along with smart traffic control, help the vehicles move with greater accuracy and speed. As a result, AGVs can seamlessly traverse complex environments without the need for human oversight.
For instance, an AGV in a manufacturing facility equipped with laser navigation can navigate through difficult layouts, accurately and reliably transporting materials.
Collision Warnings
Collision warnings are a key safety feature for AGVs. These systems use sensors, cameras, and other technologies to detect potential hazards, using warnings or initiating emergency braking to avert accidents.
For example, Cyngn’s collision avoidance system, Virtual Bumper, extends in front of our automated guided vehicles and utilizes a network of in-vehicle sensors that enables it to automatically stop and prevent collisions. Therefore, if our vehicles were in a busy warehouse, they would be able to identify objects and quickly either stop or change course altogether in response.
Types of Automated Guided Vehicles
Unit Load AGVs
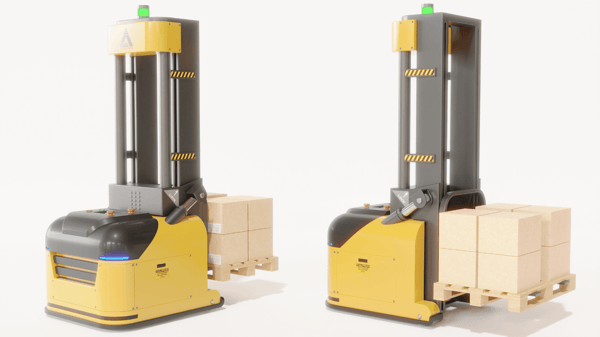
Unit load AGVs are specialized automated vehicles that handle and move large loads or palletized materials. They are equipped with advanced sensors, devices and navigation systems, allowing them to autonomously navigate and follow set routes while carrying substantial loads. You can find them most often in manufacturing and warehousing settings.
We see this a lot at Amazon, which uses unit loaders in their fulfillment centers to move pallets of products within their warehouses. These vehicles significantly speed up pickup and delivery times.
Towing AGVs
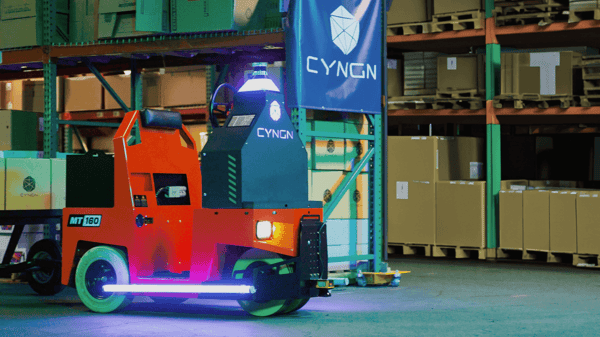
Towing AGVs, which include autonomous tuggers, are driverless robotic vehicles that tow or pull heavy carts, trailers, or other material-handling devices. These AGVs are equipped with robust towing mechanisms, allowing them to efficiently tow multiple carts at once across factory floors and warehouses. For example, Cyngn’s Automated Tugger can perform repetitive hauling workflows like transferring finished goods or delivering supplies, towing an impressive 12,000 to 20,000 lbs.
Automated Guided Carts
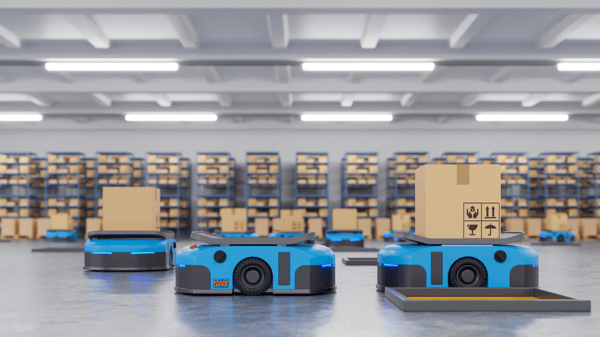
Automated guided carts (AGCs) are compact autonomous vehicles that transport materials in smaller quantities using carts or trolleys. These versatile AGVs are best for applications such as material transport and assembly line feeding.
For example, Boeing utilizes AGCs in their aircraft manufacturing facilities to move components and materials along assembly lines. By adopting AGV technology, Boeing was able to speed up their building process and increase overall precision in material handling.
Custom AGVs
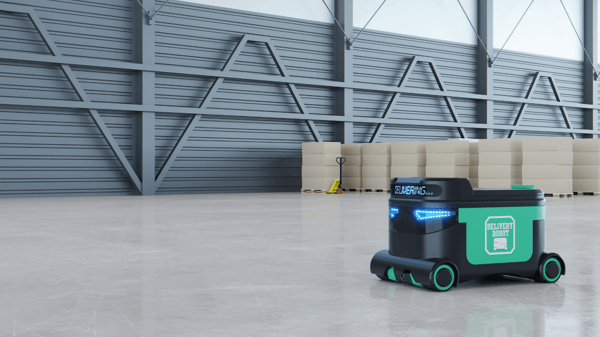
Custom AGVs offer the best personalized solutions made to tackle specific requirements and unique material handling needs. These industrial AGVs incorporate specialized features, sensors, and functionalities based on the particular demands of the application. This may include adapting the AGVs size, payload capacity, navigation technology, or integration with existing machinery. As a result, they are useful for complex settings that require unique applications.
For example, General Motors utilizes more than 75 custom industrial AGVs in their automotive manufacturing plant to deliver bulk body shop and general-assembly materials.
What are Common Applications of Automated Guided Vehicles?
Pallet Handling
AGVs find widespread application in pallet handling. These tasks include loading, unloading, stacking, and transporting pallets, which ensures an efficient material handling process throughout a facility.
For example, Global Logistics & Fulfillment, a leading 3PL provider deployed Cyngn’s autonomous stockchaser to transport pallets efficiently around their warehouse facility, leading to a substantial increase in productivity.
Work-in-Progress Movement
In work-in-progress movements, AGVs transport unfinished materials between different stages of production. For example, AGVs in work-in-progress movements typically transport materials from one point in a facility to an assembly line during the production stage. By employing AGVs, companies embracing factory automation can optimize workflow efficiency and reduce manual handling requirements during the assembly process.
Learn more about our autonomous tugger workflows
Trailer Loading
AGVs are extensively used for streamlining the loading of goods from storage areas or assembly lines to waiting trailers for shipment. These vehicles can be equipped with specialized mechanisms such as conveyor belts or lifting platforms to efficiently load pallets or containers onto trailers. As a result, AGVs enhance the speed and accuracy of loading operations, reduce manual labor, and boost overall efficiency.
For example, DHL utilizes AGVs in their logistics centers to load shipments onto trailers for transportation, which in turn, streamlines their supply chain operations.
Industries That Use Automated Guided Vehicles
Manufacturing
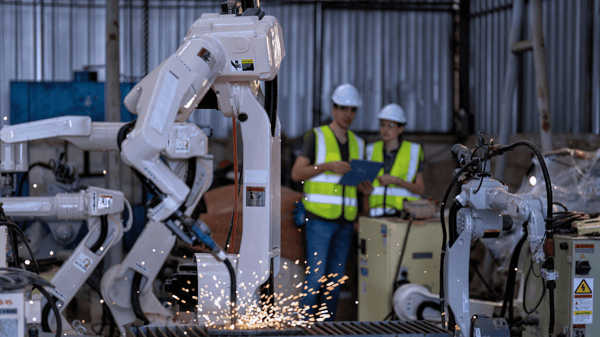
Manufacturing holds 70% of the AGV market, using them for material, work, and product transport. As a result, AGVs have been driving the creation of smart factories. Companies like Mitsubishi Electric are using AGVs in its smart factories to boost productivity and shift labor to higher-value tasks.
Warehouses
-2.png?width=600&height=338&name=AMR%20(warehouse%20trend)-2.png)
Warehouses heavily depend on AGV integration with Warehouse Management Systems (WMS). AGVs are also used for logistics like inventory, order picking, and moving goods. AGVs aid in quality control by analyzing finished products for consistency. Firms like Walmart adopt warehouse automation to enhance workflows, automating tasks like order picking and loading/unloading trucks.
Automotive
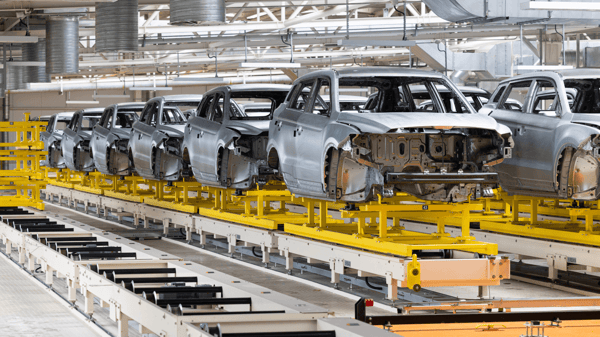
In automotive manufacturing, AGVs optimize logistics and production. For example, AGVs like automated forklifts can transport materials and aid assembly line processes. Organizations like Nissan are deploying AGV fleets in their assembly plants to boost efficiency, reduce congestion, and reallocate labor.
Agriculture
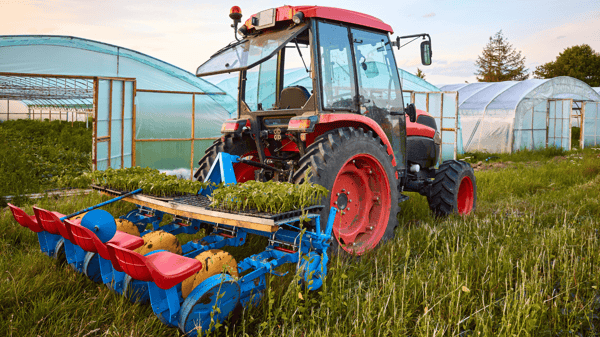
AGVs navigate in manufacturing and warehouses and are crucial in modern agriculture. They enhance efficiency, precision, and intralogistics in farming. AGVs and AMRs (Automated Mobile Robots) automate tasks like planting, harvesting, and crop maintenance with specialized tools or robotic arms.
Types of AGV Navigation
Laser Target
Laser target navigation is a common method employed by automated guided vehicles to precisely guide their movements with vision through a designated area. Laser sensors emit laser beams which bounce off the reflective targets, allowing the AGV to measure the distance and angle to each target accurately. This enables AGVs to navigate through complex paths.
Wired
In this type of navigation, AGVs follow a predetermined path marked by wires embedded in the floor or attached above it.
AGVs equipped with sensors and detectors follow the path of these wires ensuring consistent and predictable navigation. The wires emit electrical signals to the AGVs, which then serve as their guide throughout their workflow. This method is commonly used in manufacturing and warehouse environments where companies create fixed and well-defined routes for AGVs, keeping in mind that any deviations in path need to be minimized.
Magnetic
Similar to wired navigation, this method uses magnetic strips or markers embedded in the floor to guide AGVs along specific routes. Magnetic navigation is especially useful in manufacturing environments requiring flexible and easily adaptable routes, such as a warehouse where the layout tends to undergo frequent changes.
Vision
Vision-based navigation is an approach where AGVs rely on advanced imaging systems to interpret and navigate the surrounding environment. AGVs use vision sensors, such as cameras or 3D imaging devices, to capture real-time visual data to analyze and identify markers, patterns, or landmarks for reference points. As a result, vision-based navigation excels in applications where the environment may change or where a more adaptable navigation approach is needed.
Lidar
AGVs use lidar for navigation and obstacle avoidance. Lidar creates detailed 3D maps of the vehicle's surroundings, allowing it to navigate autonomously, ensuring precise localization and obstacle avoidance. For example, the lidar in Cyngn’s AGVs can see up to 30 meters and do a full scan 10 times per second. Each scan generates a rich 3D rendering, made up of 32,000 individual data points, giving our AGV system the information it needs to allow AGV fleets to make instant decisions about its surroundings.
Geoguidance
Geoguidance navigation relies on geographic information systems (GIS), GPS, and advanced positioning technology to guide AGVs. AGVs equipped with geoguidance systems use detailed maps of the given environment to compute their exact location and therefore how to best navigate throughout a facility. As a result, AGVs gain full awareness of their surroundings and can navigate safely throughout its environment.
By integrating geographic information, AGV fleet management can enable AGVs to navigate through dynamic environments with a high level of accuracy, including manufacturing plants, warehouses, and distribution centers.